This weeks tools of trade interview takes us to the hamlet of Sayville, Long Island, New York ... Sayville was founded by a man named John Edwards who built his first home there in 1761, the hamlet was accidently named 'Sayville' (it was meant to be called 'Seaville'), when the error was discovered the people wrote a letter to Washington to have it spelt correctly, that request was turned down as it was felt there were too many 'Seaville's' in the world and that 'Sayville' was unique ... speaking of unique, the very talented ceramic artist, Jill from GlazedOver is here (in Sayville) to give us an insight into the tools she uses to create her rustic and vibrant ceramics and indie jewelry. So, without further ado - let's go!

Wabi sabi nesting bowls pumpkin and blue handmade
Would you take us through the tools you use in your creative process?
I'm very grateful to say that now my creative process begins with my beloved pugger.
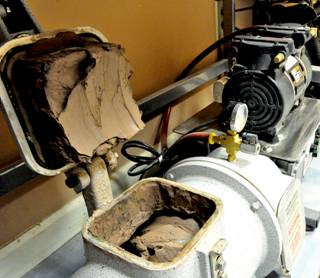
Instead of me wedging the clay manually (at the costs of my wrists), the pugger processes all of my recycled clay mixing dry with moist flawlessly and then de-airing the lot. Thanks to my pugger I can now spend my time more productively and more creatively.
There are so many ways to work clay, but I'm partial to slab built and wheel thrown work. Depending on which whim strikes me (or which custom orders are on the roster), I'll head over either to the slab roller or to the pottery wheel and the process takes off from there.

There are various small tools - like pin tools, ribbon tools, sponges, ribs, calipers, and wire tools - that are appropriate to each method and sometimes even unexpected things can be useful tools. Lace, a corn cob, a shell, or a barnacle can be used to create texture, for example. The sky's the limit!

When I've finished tweaking a piece, I set it on the drying shelf. Once it is 'bone dry' (absolutely, completely and utterly devoid of all moisture) it goes into the kiln for the bisque firing. After it comes out, I glaze it and put it back into the kiln for the glaze firing.

Often, people don't realize how time intensive clay work is. From start to finish, depending on the size and structure of the piece, it can be upwards of 3-4 weeks before the bisque firing is even appropriate.
Can you give us some sort of indication on the monetary outlay you've had in setting yourself up with the equipment that you have?
From the kiln to the wheel to the pugger to the tools ... ugh. Clay equipment is very expensive. Not including electric hook up, shelving and supplies, I've spent upwards of $10,000 on equipment over the years.
What special care and/or cleaning is required to keep your tools in optimal working order?
Well, clay dust is a biggie. Left unchecked, it can have serious effects on one's health. Other than carefully washing clay off of my tools and wheel after use, I regularly vacuum and wet mop the studio. I keep my studio as clean as I can. On a practical level, it is nice to start each day's work on a clean surface. And now that I am teaching children's classes there, it is absolutely necessary for the studio to be in top shape at all times.
Other than that, there is no real equipment upkeep except for making sure that all parts (especially kiln elements and bricks) are in working order.
Do you need to wear any kind of safety equipment when creating your items?
For mixing glaze ingredients or using kiln wash (which contain toxic elements), I wear a dual cartridge mask. For viewing progress during firing I wear heat resistant gloves and dark goggles (which also help me look really cool!).
I think I would want to own a lathe for metal work. Metal strikes me as a material that is akin to clay in as much as it can be negotiated into any shape. It needs a different kind of coaxing, but the creative thought process necessary for metal work seems compatible with the way my brain works.
Other than that, perhaps a money printing machine with 20 dollar plates. And oh yes, that special cotton paper that goes with it. That should do me.
15 comments:
Wonderful read! I love your work and humor. Thank you both for the fascinating interview.
Great interview once again!
Love your studio manager :)
better a cat than a bull in a china shop!
A pleasure to read this!
This made for such an interesting read! I love your work Jill, and your wonderful personality!
Jill, what a joy it was to read your interview and have a peek into your process.
I'm envious of your pugger machine, Jill, it just looks like it could be coaxed into mixing up cookie dough!
This all looks familiar to me, from kiln to studio manager! I love the wind chimes, they are a great path to explore and probably fun to make!
Lee/OneClayBead
Thanks for the insight of where your beautiful work begins. So glad you are able to save your wrists with a piece of equipment. Also...great place for your manager...has the perfect spot to keep an eye on you!
seeing what actually goes into the whole process of making pots takes some of the romance out, but replaces it with a healthy respect for what it takes!! wow!
Thanks, everybody! And thanks, Kerrin/Sigmosaics for giving me the opportunity
Sharon/KnotOriginal - I haven't tried cookie dough yet, but last Tuesday we made mean pistachio ice cream! ;D
Jill, i've always been a big fan of your work and I have a new appreciation of all that you do! Thanks so much for giving this insight into your work, LOVED your interview ... who wouldn't want a money making machine?! ;)
lovely to 'pop in' to your studio ~ thanks for the great interview. nice to meet your manager too :)
Loved seeing and hearing about your tools, Jill. And your glazes are beautiful, like abstract paintings.
Another great interview Kerrin! I want one of those 20 dollar printers too...
haha i remember when you were looking for a plugger :)
love your article, let me know when you get a money making machine ;)
a great read and funny too! thanks Jill - nice to find out more about your beautiful work!
Post a Comment